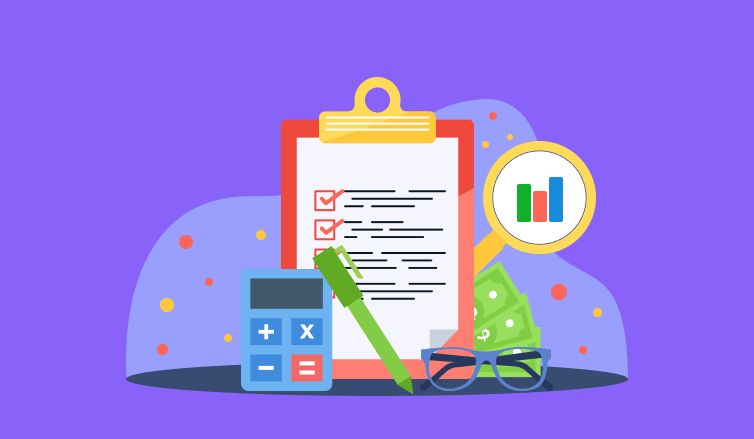
When estimating costs that your project may incur, you gain a higher chance to keep it profitable and achieve the desired performance outcomes. But how to approach cost estimation?
It would help if you started by identifying which types of expenses your project will bring about. The only issue is that there is more than one way to do this. And to keep the confusion down, here we described the six main methods that managers may use today to sort diverse kinds of costs.
Dive in to learn more!
What Are Project Costs?
Project costs are the funds required to perform a planned business endeavor, and they are a primary subject in project budgeting and cost management. Costs are the entities you estimate when developing a budget. They are the money you actually invest in work and the amounts you track and control until the very end of a project.
Main Types of Project Costs
1. Direct vs. Indirect Costs
One of the most common methods to categorize project costs is by dividing them into direct and indirect expenses.
Direct expenses are entailed by everything you do to produce a particular output. Let’s take a hardware development project as an example. In its case, direct costs will include:
- Raw materials for the creation of finished goods (e.g., steel, plastic, etc.),
- Direct labor (i.e., human resources and hours necessary to manufacture the product),
- And production equipment.
Overall, any cost that directly influences your output volume belongs to the category of direct expenses. Any change in the magnitude of production will lead to either an increase or decrease in the number of specific things needed to meet the set output goal. These things will be your direct expenses.
In contrast, indirect expenses comprise the cost of everything that isn’t directly linked to primary project operations but is required to support them.
Let’s consider the above example again. To create hardware, you need to:
- Rent a facility,
- Pay wages to administrative employees,
- Use technology for communication between business units,
- And travel to different cities to sign contracts with suppliers.
All these activities fall under the category of indirect costs. They are essential for the sustainability of the business as a whole but are not associated with the production process itself.
2. Fixed vs. Variable Costs
When categorizing expenses based on the production capacity, business practitioners divide them into fixed and variable costs.
Fixed costs are those expenses that never vary in their amount regardless of possible changes in output volumes. One of the best examples of a fixed cost is rent payment. For instance, the abovementioned hardware development company may have to pay $15,000 for a production facility monthly. This price remains the same, invariably of how many items the business has manufactured during the rent period – 15 or 500.
Conversely, variable costs constantly change as the company increases or decreases its production outputs. If the same hardware development company decides to manufacture 300 USB flash drives for the cost of $15 (i.e., the sum of all relevant direct expenses), the total variable cost for that project will be $4,500. At the same time, if this company will choose to produce 800 USB drives instead, the variable cost will go up to $12,000.
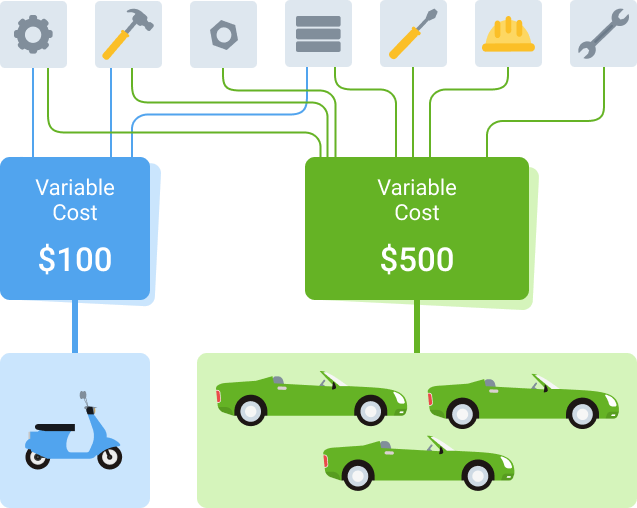
3. Period vs. Product Costs
There is yet another way to classify expenses based on their relation to the production process – by dividing them into product and period costs.
Product expenses refer to EVERYTHING involved in the production process:
- Direct costs,
- Expenses your business incurs when running its daily operations,
- Equipment maintenance,
- Salaries of production managers, etc.
Overall, this group of expenses includes a variety of objects and activities that are both directly or indirectly linked to the central process of production (or service provision) itself.
As for period expenses, they are incurred not by the purchase or production of goods or services but by time. To clarify this, let’s see how companies write off product and period costs in their balance sheets. The former group of expenses is usually reported either as inventory or as the cost of goods sold. In contrast, period costs are normally expensed in the period incurred as selling costs or general and administrative expenses that result from daily business operations. For instance, since product promotion activities, wages of administrative employees and corporate office rental are typically bound in time and aren’t in direct relation to the primary production process, they should be regarded as period costs.
Download our free detailed guide on project cost management.
4. Pre-operating vs. Operating Costs
Costs can be grouped depending on their connection to different stages of the project’s life cycle. In this way, pre-operating and operating expenses are discerned.
Pre-operating costs are incurred prior to the actual start of the project and all relevant operations. Before engaging in project realization, you may need to conduct an environmental analysis, develop a strategic plan, and train new staff members. All these preliminary activities fall under the category of pre-operating costs. Since they serve to guarantee successful completion of the project, pre-operating expenses are an essential part of the initial investment. For this reason, they must be expensed as intangible assets in the accounting documents.
Operating costs are incurred after the official start of project operations. This group of expenses comprises everything required to keep the business going, including inventory, employee wages, technology, intellectual property, rent, and funds allocated to such vital activities as marketing, sale and production. It means that both direct and indirect project expenses are considered operating costs as long as they take part in the daily maintenance and management of the project. After figuring out this type of expense as per your project’s needs, you may also use the numbers to calculate its operating income – the sum of earnings realized from project activities, after deducting all operating costs. This practice will allow you to see whether your endeavor is profitable or not.
5. Retrospective vs. Prospective Costs
Another way to look at costs is by considering their time orientation and the potential for recovery. Thereby, project expenses can be either retrospective or prospective.
Retrospective costs, also known as sunk costs, are expenses that have been incurred in the past and cannot be recovered. Since retrospective costs have already taken place, they usually are not taken into account during financial decision making. In contrast, as future expenses that haven’t yet taken place or past expenses that could be recovered, prospective costs influence decision making to a substantial degree.
Assume a publishing business that plans to issue a novel. When choosing the pricing strategy for the new book, the management thinks over the costs of materials and labor required to print a single item. Depending on the quality and price of paper and ink utilized for production, the charge for the final product will vary. At the same time, such things as a $9,000 printing equipment or a $500,000 facility that the company purchased a long time ago won’t affect the pricing decision in this situation.
Printing materials in this instance belong to the category of prospective costs since their amount could be changed as a result of the management’s ultimate decision. Contrariwise, the purchased equipment and building are sunk costs – they were committed in the past and, thus, are irrelevant to the current pricing decision.
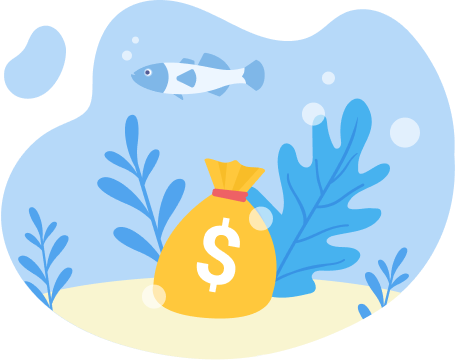
6. Opportunity Cost vs. Cost of Risk
The last category in the list – costs of opportunity and risk – is defined based on the potential outcomes of incurred expenses and their ability to produce financial benefits or loss.
Since risks frequently cause damage to the financial health of businesses, the cost of risk primarily refers to the loss of money due to the failure to foresee various environmental hazards. Nevertheless, expenses incurred when managing risks are often regarded as the cost of risk as well. Thus, besides direct financial damages induced by external influences, the total cost of risk (TCOR) comprises such activities as risk analysis, risk mitigation, risk control and all relevant administrative expenses. Therefore, by evaluating different costs of risk, you can not only predict the extent of a possible loss due to changes in the market environment but also see how effective and efficient your risk management strategy is.
As for opportunity cost, it refers to financial benefits that a business may miss because of selecting one investment alternative over another. Imagine that you have two investment options to choose from, and each of them could lead to disparate financial outcomes. To calculate an opportunity cost in this case, you would need to:
- Predict the expected return on investment per each opportunity,
- And identify the difference between their assumed returns.
This difference would be your opportunity cost. As you can tell from the provided example, this type of expense is a purely analytical concept. Nonetheless, it bears an immense value for managers because it supports the making of more informed decisions.
How to Manage Project Costs
Project cost management is the process of planning for expenses and controlling the costs of a project. It includes identifying, estimating and budgeting for all the costs associated with a project and its primary goal is to ensure that your project is completed without any major budget overruns.
There are four main steps in the project cost management process:
- Estimate costs
- Create a budget
- Track and control costs
- Close out the project and account for all final costs
Let’s look at them one by one.
1. Estimating Costs
Estimation is the process of predicting the future cost of a project. You may choose one of many different cost estimation methods to get this task done, but the most important thing is to ensure that all potential project expenses are taken into account. This includes the costs for materials, labor, overhead, etc.
There are also a number of various factors to consider when carrying out cost estimation:
- Scope of the project. You need to think of things like how many people will be working on the project, how long it will take to complete it and what kind of resources will be required.
- Nature of the project. This includes things like whether it is a new product or service or an existing one that is being modified.
- Size of the project. Determine the number of products or services that must be produced or the number of people that will be using the product or service.
The more accurate cost estimates you make, the better it is for your overall project outcomes. Accurate estimates are the key to good project planning: if you’re off by even a small amount, it can throw your whole project schedule off course. Thus, it’s better to take project estimation as seriously as possible.
2. Creating a Budget
Once the costs have been estimated, it’s time to proceed to project budgeting, i.e., to allocate funds to different aspects of a project.
To create a perfect budget, it’s essential to know not only how many expenses your project will incur but also how much money you will have at your disposal throughout the course of work. Thus, you need to analyze your income and expenses using some high-quality data. This will give you a good idea of where your project money will go and how much you will spend at different work stages.
It’s also vital to be realistic when creating your budget. Make sure to factor in the unexpected costs and leave room for some contingencies. If your budget is too tight, you’ll likely end up going over it.
3. Tracking and Controlling Costs
Once the actual work begins, costs should be closely monitored to ensure you stay within the approved budget. If expenses begin to exceed the initial estimates, you will have to undertake some steps to take them under better control. This may involve cutting back on some aspects of the project, rethinking some objectives or renegotiating contracts with suppliers or contractors. And to prevent any serious alterations to your original plans, you need to identify the risk of cost overruns early on. Hence, accurate cost tracking is critical.
So, what is the best way to track project costs?
A simple work breakdown structure template can do an excellent job for smaller and simpler projects, while the larger ones will require you to apply advanced software. But whatever method works best for you, be sure to keep track of every single expense, no matter how big or small.
With actiTIME, for example, you can easily keep a detailed record of your direct staff-related expenses. It is a perfect tool for tracking both billable and non-billable hours worked by employees. Plus, it features a few handy cost and profit reports that are helpful not only for better control over your current projects but also for estimating future ones.
To learn more about how to track project costs with actiTIME, don’t hesitate to check out this post and sign up for a free 30-day trial to give our time tracker a whirl.
4. Closing Out the Project
When the project is completed, all costs should be accounted for (including any costs that were incurred but not originally documented in the budget).
A final report on the project’s costs should be prepared and submitted to the client or sponsor. This will help you and them to understand the true cost of the project and will allow for more informed decision-making regarding future works.
Conclusion
As you can see, there is a multitude of ways to look at project costs. It is possible to characterize expenses by:
- Their contribution to the project’s output and central operations,
- Their dependence on the overall production magnitude,
- Roles they play at different stages in the project’s life cycle,
- Time they were committed,
- Their hypothetical effects on the project’s financial health, and so on.
By enriching your knowledge of varying cost categories, you increase your awareness of expense sources that could be previously overlooked. Being able to discern different types of costs involved in your project more precisely, you can enhance the accuracy of your cost estimation results to a substantial degree.