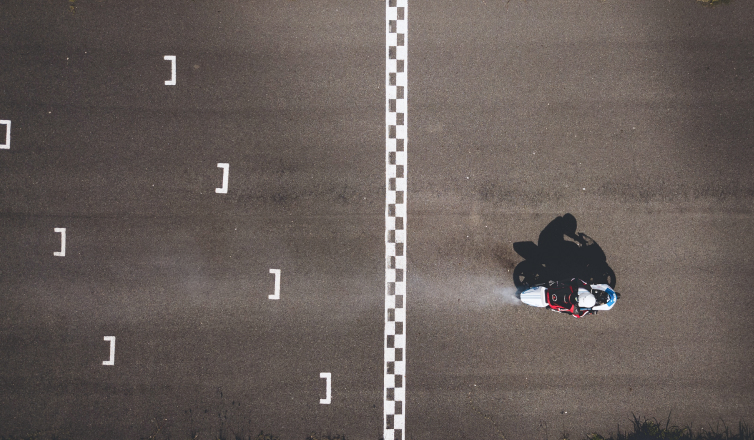
Introducing Kanban in the work routine is a significant step forward in any project management process. Being a commonly used component in the Lean methodology, it works perfectly for teams that operate on the basis of Scrum and Agile approaches. So, what is Kanban and how to use it effectively?
What is Kanban?
Kanban was introduced by Taiichi Ohno, the father of Toyota’s production system, as a way to optimize workflow and get the most value out of available resources.
Kanban system as we know it today was developed to increase the efficiency of production processes and reflected Ohno’s philosophy regarding mindful usage of production resources. His famous “seven wastes” that became the basis of Lean project management methodology and Kanban technique are:
-
Waiting
Time when products or parts are neither transported nor processed adds no value to the product, only creating costs.
-
Overproduction
Basically, this means producing items before they are actually required.
-
Unreasonably expensive processing
Using expensive or too complex tools where simpler ones would be suitable.
-
Transportation
The process of moving parts between production steps that produce no value.
-
Excessive motion
Non-ergonomic workspaces that make employees excessively move, bend, reach, lift, walk etc., which creates health and safety issues.
-
Unnecessary inventory
Excessive objects that consume physical space, create delays, and inhibit planning.
-
Quality defects
They require rework and re-inspection, creating enormous additional costs and delays.
The main purpose of the Kanban system, as it was introduced by Ohno, is to eliminate these wastes, help teams use resources more wisely, and make the work environment lean and clear. This is the main reason why Kanban is becoming increasingly popular in many industries.
Would Kanban Work for My Field and Team?
As we see, these principles are originally related to the production environment but can be adapted to nearly any complex work process. So today Lean methodology, Agile / Scrum techniques and Kanban as their essential addition are increasingly adopted in various industries, among them software development, design, consulting, and other knowledge-based fields.
Kanban brings various benefits to project managers and teams:
- It visualizes work progress and helps evaluate it faster;
- It limits the amount of work in progress, helping teams and individuals focus on accomplishing already started tasks;
- It improves workflow and makes it clearer;
- It makes problems visible, mainly it applies to the bottlenecks that are likely to appear or have already appeared;
- It shows where changes and re-prioritization are needed.
These benefits are especially relevant in customer service fields where workflows tend to become chaotic as project requirements, clients’ priorities and resource availability change. Practical experience shows that Kanban works perfectly for the environments where:
- There’s actionable feedback from customers and stakeholders;
- Changes to requirements and priorities happen often;
- Work processes are complex and include multiple clearly defined steps;
- Resources on the project team are spread thin or limited.
How Kanban System Optimizes Workflow
One of the main purposes of implementing Kanban is to make the processes clear and manageable. Besides creating a clear visual picture of current progress, Kanban introduces specific rules in the work process that add clarity and help adapt the workflow to changes. Here are general Kanban rules, applicable to virtually any industry where this technique is used:
- The later process step uses the outcome of the previous step;
- The later step defines what needs to be produced at the previous step;
- The previous step only produces what the next step needs;
- No products are produced or moved to the next step without the Kanban authority;
- No defect products are moved to the next process step: if a defect is detected, work is returned to the previous step.
These principles simplify workflow management, make the process more predictable in case of changes, and ensure a better quality of the outcome. To sum up, introducing a Kanban board in the workflow brings the following positive changes to the environments with a tendency to get chaotic:
- Predictability;
- Manageability;
- Better resource allocation;
- Ability to quickly adapt to change.
Kanban and Other Project Management Approaches
Kanban is often compared to project management techniques and methodologies: Kanban vs. Agile, Kanban vs. Scrum, or Kanban vs. Lean. However, the “versus” framing is hardly correct here: Kanban is just a tool for implementing and using these techniques. It helps visualize work structure and simplifies work organized in sprints.
The metaphor of a lens seems to be a much more accurate way to describe the combination of Kanban and project management techniques. Kanban is something you choose to see through and use to focus on what’s important for you – just like a lens, it enhances workflow aspects that require closer attention.
That said, Kanban can bring some modifications to the established techniques. For example, while the traditional Scrum approach doesn’t imply changes in the middle of a sprint, Kanban makes it possible. What’s more, Kanban creates a convenient environment for self-organizing teams that are one of the basic concepts of Agile and Scrum. Clear workflow, constant availability of the big picture for any team member, and high responsiveness to changes make Kanban a perfect addition to Agile processes.
Automating Workflow with Kanban Software
Besides bringing visualization and organization benefits to the work management process, Kanban has turned out to offer convenient ways to automate work. An electronic version of the Kanban board is being included in many project management software solutions as a useful addition to the basic features. Kanban modules and tools are often convenient for both managers and regular employees – and here’s how:
- They minimize organization efforts, saving managers’ time;
- They immediately show problematic areas in the workflow, allowing managers to proactively tackle possible issues;
- They help achieve a better outcome and improve quality of work;
- They increase engagement of regular employees, showing the big picture of the work progress and their particular roles in it;
- They allow to take stakeholders’ feedback into account at virtually any step, making the process more responsive to changes;
- They allow to save team’s resources and deliver results faster.
Today, Kanban systems are available in almost all project management tools, as well as in work management and timekeeping solutions. Team and project managers can use them as a primary tool or just for reference, to stay informed on the progress – the key idea is saving efforts on work status monitoring.
Final Thoughts
When determining whether Kanban would work for your team and is worth implementation, analyze your expectations and needs within the framework you’re using for project management. You can use the experience of similar projects or teams to see how Kanban influenced their workflow, performance, and outcome.
Knowing why you’re implementing it, select the right tool for your needs that would fit into your workflow routine and provide you with all essential work process data in the visual form. Configure your Kanban system according to your specific requirements, and start saving resources and getting more work done.